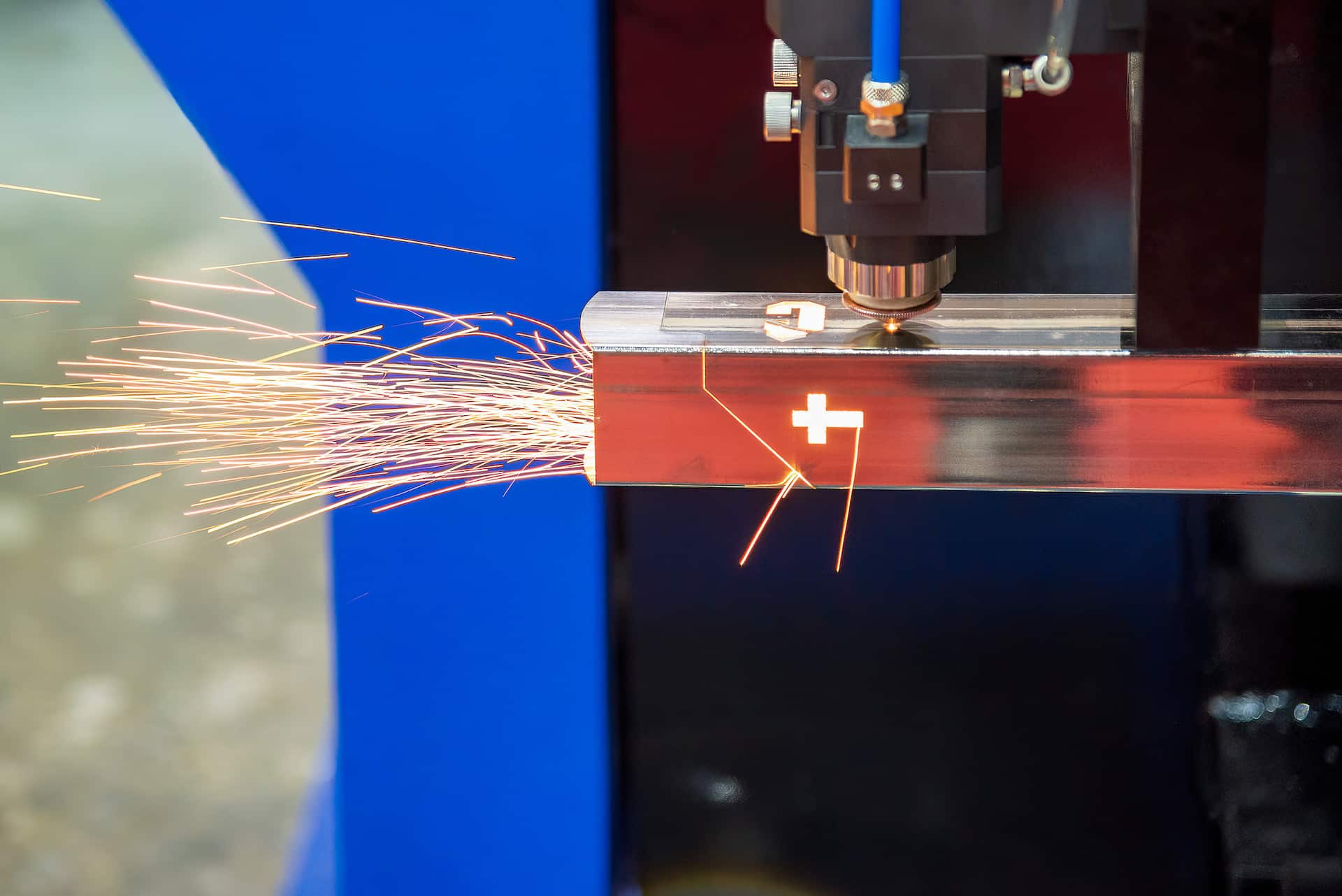
Laser Rust Removal
In contrast, citric acid passivation and electropolishing go beyond surface cleaning to enhance the metal’s natural corrosion resistance, offering far superior protection, especially after processes like laser cutting that can damage the metal’s surface integrity.
What Is Laser Rust Removal?
Laser rust removal uses a focused beam of light to vaporize or ablate contaminants like rust, paint, or oxides without the need for chemicals or abrasive blasting. It’s an effective method for surface cleaning when delicate handling or tight tolerances are required.
Advantages of laser rust removal include:
-
Non-contact process that minimizes surface wear
-
Highly precise control over removal depth
-
Environmentally friendly (no chemical runoff or blasting media)
-
Lower risk of mechanical damage compared to abrasive methods
However, while laser rust removal effectively cleans a surface, it does not address the deeper metallurgical changes that occur during manufacturing processes like laser cutting, nor does it regenerate the stainless steel’s crucial passive layer. Learn more about why does stainless steel rust?
How Manufacturing Processes Affect the Corrosion Resistance of Stainless Steel
The exceptional corrosion resistance of stainless steel comes from its thin, invisible chromium oxide layer—a passive film that forms naturally when the metal is exposed to oxygen. This protective layer is what shields the underlying metal from rust, pitting, and other forms of corrosion.
However, many common manufacturing processes can disrupt or damage this critical passive layer, including:
-
Laser cutting: Intense localized heat can burn off the chromium oxide film near cut edges and alter the microstructure in the heat-affected zone (HAZ). It can also introduce contaminants like free iron through oxidation or cross-contamination.
-
Machining and grinding: Mechanical operations can smear free iron across the surface or embed particles into the material, creating potential corrosion initiation sites.
-
Welding: High temperatures during welding can destroy the passive layer and cause heat tinting—visible oxide discoloration that significantly reduces corrosion resistance if not properly removed.
-
Forming and stamping: Deformation processes can create microscopic defects, strain-harden the surface, and expose fresh metal that lacks a mature passive layer.
-
Pickling and cleaning errors: Incomplete or improper chemical treatments can leave residues or expose the surface to further contamination.
Without proper secondary treatments, areas affected by these processes become vulnerable to localized corrosion such as pitting, crevice corrosion, and rust—even if the rest of the stainless steel part remains intact.
Simply cleaning the surface is not enough.
To fully restore and maximize corrosion resistance, the surface must be passivated—a process that removes contaminants and rebuilds the stainless steel’s essential chromium oxide layer. What is passivation?
Why Citric Acid Passivation and Electropolishing Are Superior
Unlike laser rust removal, citric acid passivation and electropolishing remove surface contaminants and restore the passive chromium oxide layer, ensuring true corrosion resistance is re-established.
Citric Acid Passivation
Citric acid passivation is a chemical process that:
-
Cleans the stainless steel surface of heat-affected contaminants and free iron
-
Promotes the formation of a new, robust chromium oxide layer
-
Restores or enhances the material’s natural corrosion resistance
Benefits of citric acid passivation:
-
Environmentally friendly and safer than nitric acid passivation
-
Highly effective even for laser-cut parts
-
Essential for industries like medical, aerospace, food processing, and marine
-
Compliant with ASTM A967 and other stringent standards
In short: citric acid passivation doesn’t just clean the surface—it rebuilds stainless steel’s essential defense against corrosion.
Electropolishing
Electropolishing further enhances the surface by:
-
Microscopically smoothing out surface irregularities
-
Removing embedded contaminants
-
Producing a bright, clean, highly corrosion-resistant finish
Electropolished parts exhibit:
-
Superior aesthetics
-
Enhanced cleanability (critical for hygiene-sensitive industries)
-
Reduced surface roughness, minimizing sites where corrosion can start
Electropolishing (sometimes referred to as electrochemical polishing) or Citric Acid Passivation offer a comprehensive finishing solution that laser rust removal alone simply cannot match.
Why True Passivation Matters
Passivation isn’t a cosmetic process—it’s essential to the performance and longevity of stainless steel parts, especially after laser processing. Without restoring the chromium oxide layer, parts are vulnerable to:
-
Premature corrosion
-
Costly part failures
-
Product recalls and compliance risks
-
Higher long-term maintenance costs
Industries that demand absolute reliability—such as medical devices, aerospace, semiconductors, pharmaceuticals, and marine equipment—cannot afford to skip proper surface treatment.
Conclusion
While laser rust removal can clean the surface of stainless steel, it does not passivate it.
For applications where true corrosion resistance is non-negotiable, citric acid passivation and electropolishing are the superior choices. They restore and enhance the stainless steel’s natural protective layer, ensuring long-term performance and durability—even after laser cutting.
At New England Electropolishing, we specialize in helping manufacturers protect and elevate their stainless steel parts through expert citric acid passivation and precision electropolishing. Don’t just clean your parts—passivate them. Your product’s success depends on it.
Electropolishing Resources
What is Electropolishing?
Electropolishing is an electrochemical and reverse plating process that removes the outer layer of skin on a metal...
The Electropolishing Process
The electropolishing process is initiated by immersing a metal part into a temperature-controlled bath of electrolyte...
Benefits of Electropolishing
Curious about the benefits of putting your parts through the electropolishing process? Read along below where we...
How Much Material Does Electropolishing Remove?
Electropolishing, when done properly is a highly controllable process which removes as little as...
How Much Will Electropolishing Improve the Surface Finish of My Part?
Ra and RMS are both representations of surface roughness. Ra is calculated as the roughness average of a surface’s...
Electropolishing Frequently Asked Questions
Learn the difference between electropolishing and electroplating as well as how the electropolishing process works...
What is ASTM B912?
ASTM B912 is an industry standard for the passivation of stainless steel alloys through electropolishing...
What is ASTM A967?
ASTM A967 is an industry standard specification for the chemical passivation treatments for stainless...
What is ISO 13485?
ISO 13485 is a standard that applies specifically to medical devices. ISO 13485 is designed to be...