Understanding 303 Grade Stainless Steel
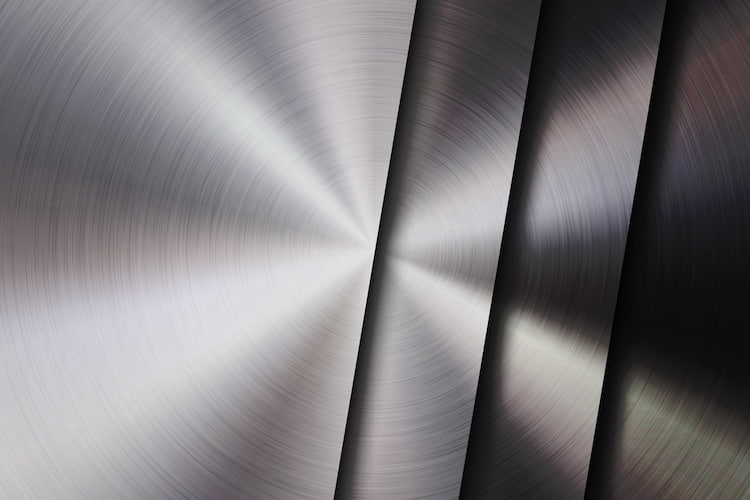
What is 303 Grade Stainless Steel?
303 stainless steel is part of the 300-series of austenitic stainless steels, containing about 17-19% chromium and 8-10% nickel, similar to other grades like 304. However, 303 distinguishes itself with the addition of sulfur or selenium, which improves its machinability but slightly reduces its corrosion resistance when compared to grades like 304 and 316.
Due to its ease of fabrication, 303 is commonly used in the production of small, complex parts and components that require extensive machining, such as screws, bolts, and gears.
History of 303 Stainless Steel
The evolution of stainless steel began in the early 1900s when engineers discovered that adding chromium to steel produced a corrosion-resistant alloy. As industries grew more complex, the need for more machinable stainless steels became apparent. To meet this demand, 303 stainless steel was developed by adding sulfur to 304 stainless steel to improve its machinability. It has since become a popular material in industries requiring rapid and precise fabrication of parts, especially in the fastener and component manufacturing sectors.
Advantages of 303 Grade Stainless Steel
- Excellent Machinability: The standout feature of 303 stainless steel is its exceptional machinability, especially compared to other austenitic stainless steels. The addition of sulfur significantly enhances the alloy’s ability to be cut and shaped, making it ideal for high-speed machining processes.
- Corrosion Resistance: While the corrosion resistance of 303 is lower than other 300-series stainless steels, it still offers good resistance to mild corrosive environments. This makes it suitable for many general-purpose applications where corrosion isn’t a primary concern.
- Good Mechanical Properties: 303 provides solid strength and durability, with a good balance of tensile strength and toughness, which ensures its utility in a wide range of manufacturing applications.
- Ease of Fabrication: In addition to its machinability, 303 stainless steel can be readily formed and fabricated into different shapes, making it versatile for various applications.
Disadvantages of 303 Grade Stainless Steel
- Reduced Corrosion Resistance: The sulfur that improves machinability in 303 stainless steel also reduces its overall corrosion resistance, especially in chloride-rich environments. For applications where corrosion resistance is more critical, other grades like 304 or 316 are better suited.
- Limited Weldability: Due to the presence of sulfur, 303 stainless steel is not recommended for applications that require extensive welding. The sulfur can cause hot cracking, and welded parts may suffer from reduced corrosion resistance in the heat-affected zones.
- Not Suitable for High-Temperature Applications: 303 grade is not ideal for applications involving prolonged exposure to high temperatures. Other grades, such as 321 or 316, offer better heat resistance.
- Slightly More Brittle: The inclusion of sulfur can also make 303 slightly more brittle than other austenitic grades, which might not be ideal for applications requiring high ductility.
Common Applications of 303 Grade Stainless Steel
303 stainless steel’s primary advantage is its machinability, which makes it a popular choice for producing parts that require extensive and precise machining. Common applications include:
- Fasteners: 303 is frequently used for manufacturing screws, bolts, nuts, and other fasteners that require precision machining but do not require high levels of corrosion resistance.
- Gears and Shafts: The excellent machinability of 303 makes it ideal for producing gears, shafts, and other rotating parts that need to be fabricated quickly and efficiently.
- Aircraft Fittings: While corrosion resistance is important in aerospace, 303 is sometimes used in aircraft fittings where high machinability and moderate corrosion resistance are sufficient for non-critical components.
- Electrical Components: 303 stainless steel is often used in the production of electrical components, connectors, load cells, and terminal fittings due to its machinability and strength.
- Valve Bodies and Pump Shafts: Components such as valve bodies, pump shafts, and other parts that require complex shapes and machining benefit from 303’s machinability.
- Automotive Components: In the automotive industry, 303 is commonly used to make small, precision-machined components like bushings, brackets, and fittings that do not require high corrosion resistance.
Conclusion
303 grade stainless steel is an excellent choice for applications that demand high levels of machinability, making it a go-to material for industries that require the rapid and efficient fabrication of small, intricate parts. Although it doesn’t offer the same level of corrosion resistance as other austenitic grades, 303 still performs well in mild environments and is suitable for a wide range of general-purpose applications.
Whether you’re manufacturing screws, gears, or electrical components, 303 stainless steel offers a combination of ease of fabrication and solid mechanical properties. However, for applications requiring higher corrosion resistance, other grades like 304 or 316 might be more appropriate.