Understanding 321 Grade Stainless Steel
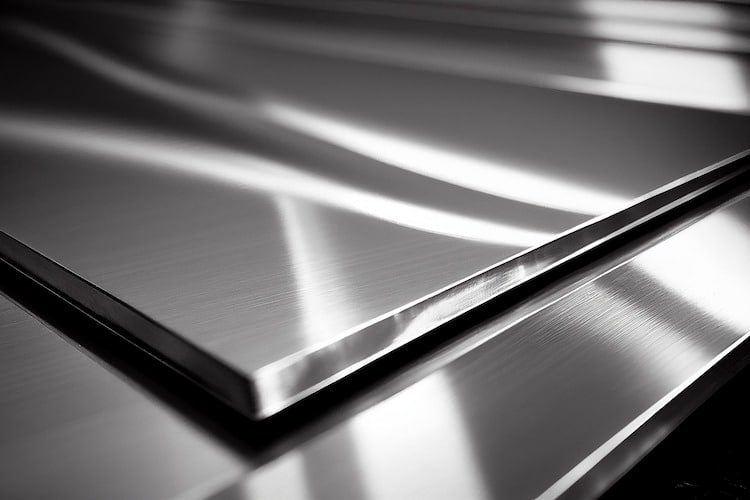
What is 321 Grade Stainless Steel?
321 stainless steel is a titanium-stabilized stainless steel with a composition that includes approximately 17-19% chromium, 9-12% nickel, and trace amounts of carbon. What sets it apart from other grades is the addition of titanium, which improves the steel’s resistance to carbide precipitation during welding or exposure to high temperatures. This makes it a go-to material for applications requiring good weldability and resistance to high temperatures.
The 321H variant is a high-carbon version of 321 that provides enhanced strength at elevated temperatures, which is useful in environments where both strength and thermal stability are critical.
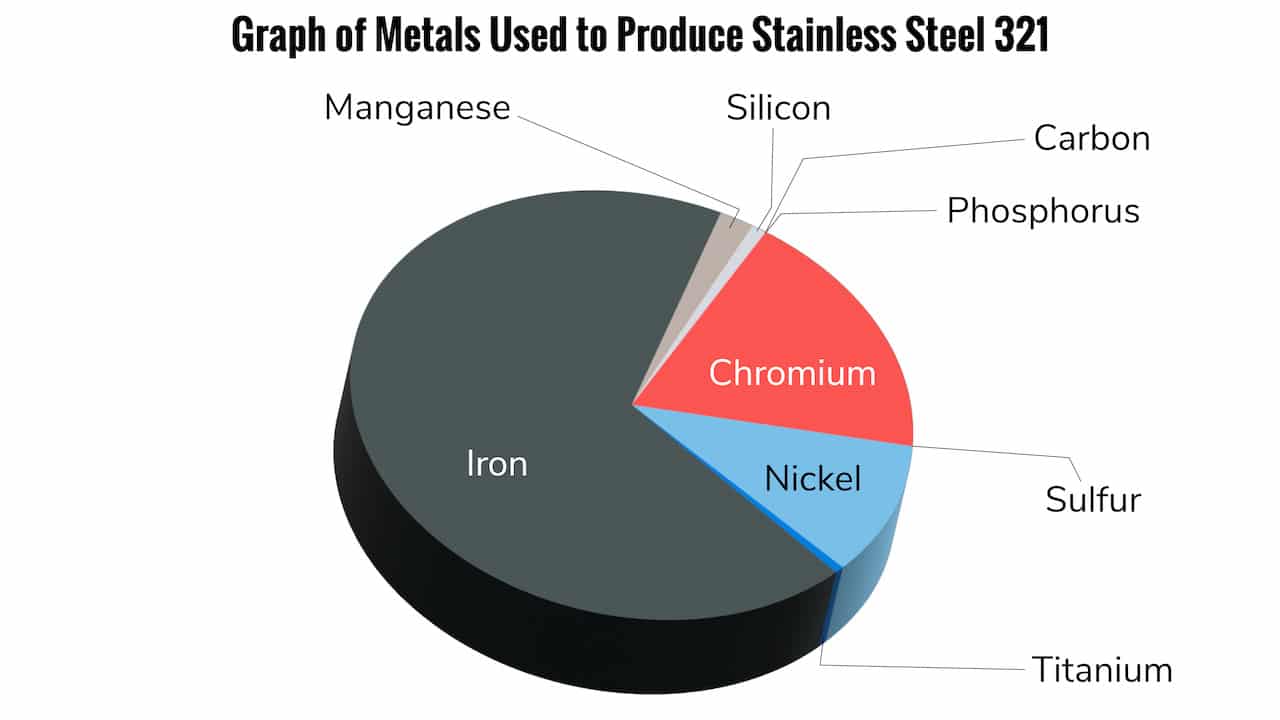
History of 321 Stainless Steel
The history of stainless steel began in the early 1900s when metallurgists discovered that adding chromium to steel could enhance its corrosion resistance. As industries evolved and required materials that could withstand higher temperatures without losing their resistance to corrosion, 321 stainless steel was developed. The addition of titanium allowed this grade to resist sensitization, a problem where chromium carbides form at grain boundaries during welding or prolonged heat exposure. This issue can lead to reduced corrosion resistance in other grades like 304 grade stainless steel, making 321 a significant innovation for high-heat and weld-heavy environments.
Advantages of 321 Grade Stainless Steel
-
Resistance to Intergranular Corrosion: One of the key advantages of 321 stainless steel is its resistance to intergranular corrosion. The titanium in the alloy prevents the formation of chromium carbides at the grain boundaries, which commonly occurs in grades like 304 when exposed to temperatures between 800°F and 1500°F. This resistance ensures that 321 maintains its corrosion resistance even after welding or prolonged high-temperature exposure.
-
High-Temperature Strength: 321 can withstand temperatures up to about 1500°F, making it suitable for high-heat applications where oxidation resistance is critical. Its high creep and stress rupture properties also ensure stability under long-term exposure to heat.
-
Good Weldability and Formability: Like other austenitic stainless steels, 321 is easily formed and welded, making it a versatile material for manufacturing and industrial processes. It can be used in both welding-heavy environments and applications requiring complex shapes.
-
Oxidation Resistance: 321 offers good oxidation resistance, making it suitable for use in environments exposed to elevated temperatures and oxidizing atmospheres.
Disadvantages of 321 Grade Stainless Steel
-
Cost: The addition of titanium in 321 makes it more expensive than basic grades like 304. For applications where high-temperature resistance and weldability aren’t essential, other less expensive options might be more cost-effective.
-
Not Ideal for Low Temperatures: While 321 stainless steel excels in high-temperature environments, it is less suitable for applications involving extremely low temperatures. In such environments, 304 or 316 stainless steel may perform better due to their increased toughness at cryogenic temperatures.
-
Limited Corrosion Resistance Compared to 316: While 321 has excellent resistance to intergranular corrosion and oxidation, it does not have the same level of general corrosion resistance as 316, particularly in chloride-rich environments.
Common Applications of 321 Grade Stainless Steel
Thanks to its ability to withstand high temperatures and resist sensitization, 321 stainless steel is commonly used in applications that involve prolonged heat exposure or frequent welding. Common industries and applications include:
-
Aerospace Industry: 321 stainless steel is frequently used in aircraft components such as exhaust systems and engine parts that are exposed to high temperatures. Its resistance to oxidation and strength retention at high temperatures makes it ideal for this purpose.
-
Chemical Processing Equipment: 321 stainless steel is often used in chemical processing plants where equipment needs to withstand high temperatures and corrosive substances. It is ideal for heat exchangers, pressure vessels, and storage tanks.
-
Thermal Equipment: Boilers, heat exchangers, and furnace parts often utilize 321 stainless steel because of its excellent resistance to heat and oxidation. It is commonly found in industrial heat-treating equipment.
-
Petroleum and Refining Industry: The petroleum industry benefits from 321 stainless steel for its ability to withstand high temperatures and resist corrosion, making it suitable for equipment such as piping, heat exchangers, and refining equipment.
-
Automotive Exhaust Systems: 321 stainless steel is used in automotive exhaust systems due to its ability to endure extreme heat and exposure to exhaust gases, prolonging the lifespan of exhaust components.
-
Expansion Joints: The flexibility and high-temperature resistance of 321 make it a good choice for expansion joints, which are used in systems that require thermal expansion and contraction.
Conclusion
321 grade stainless steel stands out for its ability to resist intergranular corrosion, its high-temperature strength, and its good weldability. While it may come at a higher cost and lacks some of the corrosion resistance of 316 grade stainless steel in certain environments, its benefits in high-heat and weld-heavy applications make it a critical material for industries like aerospace, chemical processing, and automotive manufacturing. Whether in aircraft exhaust systems, chemical processing equipment, or thermal expansion joints, 321 stainless steel is a reliable and versatile material for demanding environments.